Australia’s productivity growth averaged only 0.9% per year over the 20 year period to 2022, and it has now dropped into negative so much that our average wealth declined by nearly 9% in the past 3 years, the worst performing country in the developed world. Everyone else is becoming more efficient, and we need to […]
Read more...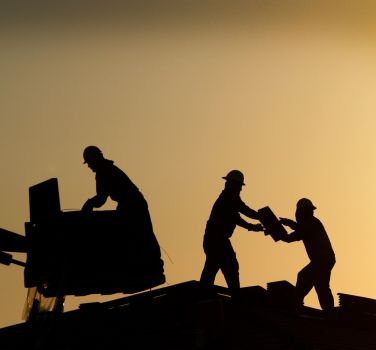